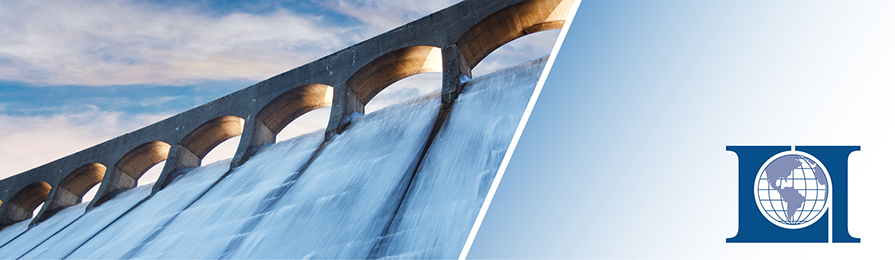
The Schedule Basis Memorandum: Key Supporting Documentation for a CPM Schedule Analysis
This article discusses general topics that should be included in a schedule basis memorandum, including the consideration of typical causes of delays that often occur on large and complex EPC projects.
1. INTRODUCTION
According to the Project Management Institute’s Project Management Body of Knowledge (PMBOK® Guide), “Project Time Management includes the processes required to manage timely completion of the project.”1 A key tool used in Project Time Management is the Critical Path Method (CPM) schedule. For large and complex Engineering, Procurement, and Construction (EPC) projects, the success or failure of Project Time Management processes is directly dependent on the validity of the CPM schedule model. Thus, it is important that the CPM schedule model is reasonable, accurate, supportable, and sufficiently detailed to provide the Project Management team with a reliable tool to appropriately plan, monitor, and make critical project decisions. No matter what level of schedule detail (i.e., Level 1, Level 2, or Level 3), the supporting documentation of any CPM schedule should include a thorough schedule basis memorandum.
All too often, however, a contractor’s schedule basis memorandum is too vague and lacks the appropriate detail needed to effectively communicate the assumptions and rationales utilized to develop the CPM schedule file. In many cases, no documented schedule basis memorandum exists. In such cases, the schedule basis assumptions can only be reconstructed from the collective and often incomplete memories of the project team members involved in preparing the CPM schedule, which is not good scheduling practice. This article discusses general topics that should be included a schedule basis memorandum including the consideration of typical causes of delays that often occur on large and complex EPC projects.
2. THE SCHEDULE BASIS DEFINED
The schedule basis memorandum is broadly defined as a written document that describes, explains, and details how a CPM schedule was developed at a specific point in time. It is usually included or referenced within the schedule management portion of a Project Execution Plan (PEP) by the contractor or by the owner. Depending on a project’s size, scope, and complexity, a schedule basis document could be presented in a simple one-page bullet format or a small number of presentation slides. For large and complex EPC projects, the schedule basis is usually detailed in a multi-section report along with supporting tables, attachments, and exhibits. A key purpose of the schedule basis memorandum is to document detailed assumptions, exclusions, and/or qualifications known at the time that the project schedule is developed.
The schedule basis memorandum is typically prepared during the baseline schedule development phase, but the schedule basis documentation should be considered as a living document to be updated periodically throughout a project’s lifecycle when conditions are warranted (e.g., re‑baseline schedule or recovery schedule development). In general, it is recommended to include sufficient detail in the schedule basis memorandum. Greater detail documenting what is known and what is not known at the time the schedule basis is developed provides better visibility of potential schedule issues or risks. A detailed schedule basis memorandum provides crucial information to key stakeholders and project participants, especially if changes substantially alter the original schedule basis plan or the original project baseline schedule becomes delayed.
3. INFORMATION TO INCLUDE IN A SCHEDULE BASIS MEMORANDUM
Two AACE International publications provide valuable input regarding the general topics to be included in a schedule basis document.2 Consistent with these publications, the major subject headings for a schedule basis memorandum should include an introduction, an overall executive summary, a discussion of the current project status, a basis of schedule assumptions for the major phases or areas of the work, and an assessment of schedule risks. Table 3-1 provides a sample Table of Contents of typical section headings for a schedule basis memorandum.
Table 3-1
Sample Table of Contents for a Schedule Basis Memorandum
Section Number | Section Title |
1.0 | INTRODUCTION |
2.0 | EXECUTIVE SUMMARY |
3.0 | CURRENT PROJECT STATUS |
4.0 | BASIS OF SCHEDULE |
5.0 | RISK ANALYSIS |
6.0 | SUPPORTING APPENDICES, ATTACHMENTS AND EXHIBITS |
The detail and depth of discussion for each of the above sections depends on the size and scope of the project. For example, a small-scope project with a short planned duration may not require a detailed schedule basis discussion. Moreover, if the contractor is developing a baseline schedule, not much discussion may be necessary for Section 3, Current Project Status, when the project has not recorded any progress. In contrast, large and complex EPC projects usually require a more in‑depth schedule basis document that provides substantially more detailed explanations and discussions. Table 3-2 presents a sample expanded Table of Contents for potential topics to include in a robust schedule basis memorandum.
Table 3-2
Sample Expanded Table of Contents for a Robust Schedule Basis Memorandum
Section Number | Section Title |
1.0 | INTRODUCTION |
2.0 | EXECUTIVE SUMMARY |
2.1 | Purpose of Document |
2.2 | Overall Schedule Information |
2.3 | Analysis of the Critical and Near-Critical Paths |
2.4 | Analysis of Risks |
2.5 | Key Assumptions, Allowances, and Exclusions |
3.0 | CURRENT PROJECT STATUS |
3.1 | Permitting Status |
3.2 | Engineering Status (Current and Forecasted Quantities) |
3.3 | Procurement Status |
3.4 | Module Fabrication Status |
3.5 | Transportation Status |
3.6 | Custom Clearance Status |
3.7 | Construction Status |
3.8 | Turnover Status |
3.9 | Commissioning and Startup Status |
3.10 | Interface Status |
3.11 | Change Order Status |
3.12 | Risk Register Status |
4.0 | BASIS OF SCHEDULE |
4.1 | General Issues |
4.1.1 | Owner Reviews and Approvals |
4.1.2 | Basis of Durations |
4.1.3 | Use of Constraints |
4.1.4 | Float Utilization (i.e., Early Dates versus Late Dates) |
4.1.5 | Schedule Calculation Mode (i.e., Retained Logic versus Progress Override) |
4.1.6 | Roll Up of Detail |
4.1.7 | Resource Loading and Equipment Utilization |
4.2 | Engineering Basis |
4.2.1 | Assumptions and Allowances |
4.2.2 | Exclusions |
4.3 | Procurement Basis |
4.3.1 | Long Lead Items |
4.3.2 | Assumptions and Allowances |
4.3.3 | Exclusions |
4.4 | Module Fabrication Basis |
4.4.1 | In-Country Module Program |
4.4.2 | Out-of-Country Module Program |
4.4.3 | Assumptions and Allowances |
4.4.4 | Exclusions |
4.5 | Transportation Basis |
4.5.1 | Bulk Materials and Equipment |
4.5.2 | Module Transportation |
4.5.3 | Custom Clearance |
4.5.4 | Assumptions and Allowances |
4.5.5 | Exclusions |
4.6 | Construction Basis |
4.6.1 | Productivity Analysis |
4.6.2 | Camp Facilities and Bed Space Analysis |
4.6.3 | Heavy Lifts |
4.6.4 | Scaffolding |
4.6.5 | Assumptions and Allowances |
4.6.6 | Exclusions |
4.7 | Project Calendars |
4.7.1 | Work Calendars |
4.7.2 | Holidays |
4.7.3 | Inclement Weather Calendars |
4.7.4 | Assumptions and Allowances |
4.7.5 | Exclusions |
4.8 | Duration Contingencies |
4.8.1 | Assumptions and Allowances |
4.8.2 | Exclusions |
4.9 | Change Order Impacts |
4.9.1 | Approach and Methodology |
4.9.2 | Assumptions and Allowances |
4.9.3 | Exclusions |
4.10 | Concerns and Other Issues |
5.0 | RISK ANALYSIS |
5.1 | Approach and Methodology |
5.1.1 | Qualitative Risk Assessment |
5.1.2 | Quantitative Risk Assessment (i.e., Duration Uncertainty and Risk Events) |
5.2 | Analysis Results and Comparisons (i.e., Deterministic, P50, P70 & P90) |
5.3 | Assumptions and Allowances |
5.4 | Exclusions |
6.0 | SUPPORTING APPENDICES, ATTACHMENTS AND EXHIBITS |
In general, more detail is better when creating basis of schedule documents for large and complex EPC projects. Even if no discussion is needed for a particular sub-section, an added benefit of the expanded Table of Contents for a robust basis of schedule document is that it also serves as a de facto check list for the contractor and owner to further ensure that all relevant topics have been addressed, when applicable. It also serves as a reminder to evaluate these topics as to whether the basis of schedule document needs updating during the course of project execution.
4. SCHEDULE BASIS CONSIDERATIONS FOR COMMON RISKS THAT MAY CAUSE DELAY ON LARGE AND COMPLEX EPC PROJECTS
Certain risks are inherent in performing large and complex EPC projects that often result in claims and disputes between the contractor and the owner. These inherent risks should be thoroughly addressed when developing a basis of schedule document for executing a project. Many of the sections and sub-sections identified in Table 3-2 require detailed consideration to properly document the Schedule Basis. The following are examples of items that should be examined closely during schedule development to ensure that the planned project completion date is feasible and that potential requests for time extensions due to alleged delays can be properly evaluated against a reasonable baseline:
- Labor Productivity Assumptions
- Competing Project Considerations
- Potential Owner Delays in Providing Review Comments
- Weather Considerations
- Camps Size Considerations
- Camp Catering and Other Service Considerations
It is recommended that the schedule basis memorandum document detailed assumptions for these issues. If a claim or dispute arises from one or more of the above issues, the schedule basis memorandum documents what was known or not known at the time of the CPM schedule development, and what assumptions or allowances were considered. In fact, the schedule basis memorandum could be the deciding document to either validate or discredit a contractor’s claim against an owner. The following sections discuss these schedule basis considerations to promote awareness for both contractors and owners regarding potential claims and disputes.
4.1 LABOR PRODUCTIVITY ASSUMPTIONS
An EPC contractor’s estimated labor productivity is a significant factor for determining the labor requirements needed to develop activity durations. Productivities should be based on: 1) a contractor’s experience in performing work in the project location or as close in proximity as possible, and 2) the availability and skills of the labor to be utilized for the project. If the labor productivity assumptions are overly optimistic, then the durations of construction activities will likely be too short and the actual duration will become extended resulting in schedule delays. For example, if durations for construction work are based on an average productivity factor of, say, 1.7 compared to U.S. Gulf Coast, and the actual productivity turns out to be 3.4 rather than 1.7, then the planned durations will be 50 percent shorter than required from the outset and the actual construction work may take twice as long as planned to perform.
Therefore, it is vital that both the EPC contractor and owner fully understand the productivity factors used in the schedule basis for developing activity durations. If the owner believes that the EPC contractor’s estimated labor productivity factors for the project are overly optimistic as documented in the schedule basis, then the owner should request that the EPC contractor prepare alternative schedules and manpower loadings using a range of productivity factors that may depict a more appropriate and realistic schedule basis for the project.
4.2 COMPETING PROJECT CONSIDERATIONS
A potential risk exists when a project is planned to be constructed in competition with other projects being constructed in the nearby area at the same time. For example, the potential for interferences and delays from other projects due to contractors’ competition for limited labor resources from the local community labor pools, suppliers, and subcontractors could impact a contractor’s ability to complete the project within its bid costs and planned duration. In addition, other contractors’ competition for use of limited construction equipment available at and near the project site could also jeopardize a contractor’s least-cost performance and planned durations.
Thus, the schedule basis memorandum should communicate to the project stakeholders what considerations have been included and document any assumptions, allowances, and exclusions regarding competing projects in the area. If the actual conditions are vastly different from what the contractor originally anticipated, as documented in the schedule basis, then a contractor may have a legitimate basis for a recoverable change from the owner. It is recommended that the contractor and owner use the schedule basis as a tool to reach agreement and understanding regarding how the schedule completion date would be adjusted if sufficient resources are not available due to competition from other projects in the area.
4.3 POTENTIAL OWNER DELAYS IN PROVIDING REVIEW COMMENTS
On large EPC projects, the owner’s and contractor’s personnel are often not co-located during the project design phase. This separation may complicate and delay the owner’s design review and approval of the work. Typical contract provisions require the owner to comment on the contractor’s submissions within a given time period, such as within 14 calendar days of owner’s receipt of the documents. If the owner is late in providing timely review comments and approvals in excess of the stipulated review time, the possible schedule delay may be detrimental to both parties.
Therefore, to mitigate potential misunderstandings between the contractor and owner, it is recommended that a robust schedule basis memorandum identify the schedule activities that require owner review comments or approvals within a stipulated review time. For large EPC contractor-submitted packages, the schedule basis memorandum should document the appropriate review time needed by the owner as well as the size of the submittal package. For example, the schedule basis document may reflect the agreement reached between the contractor and owner regarding submittal packages that can reasonably be reviewed in the agreed time period, say 14 days (e.g., not all P&IDs at once). Furthermore, the schedule basis memorandum could establish a limit on the number of packages that can be submitted per week by the EPC contractor without the owner having the right to receive additional review time.
4.4 WEATHER CONSIDERATIONS
Lost time due to unusually severe weather conditions almost always cause schedule delay. Schedule impacts and delays may stem from days lost due to severe rain, lightning, high-wind conditions, snow, ice, and extreme cold or hot temperatures. Secondary impacts to productivity could include flooding, muddy conditions, power outages, and repairing damage to installed work. Most prudent contractors include a factor for lost weather days in the bid costs and baseline schedule for normal weather conditions experienced in the project location. However, the contractor and owner often disagree on the reasonable number of lost days due to normal inclement weather that should have been included in a prudent contractor’s bid costs and baseline schedule.
It is not unusual for a contractor to use more optimistic predictions for good weather conditions. In contrast, an owner may believe that the contractor should have been more pessimistic and included more inclement weather days. Such disputes may also concern Force Majeure events stemming from flooding, lightning, hurricanes, or other acts of God. Unless contractually stipulated, a reasonable method for estimating the number of lost work days is to use a statistical average of the historical weather conditions for a particular work location based on either a 5, 10, or 15-year period.
Therefore, it is highly advisable for a contractor to document its weather assumptions in the schedule basis memorandum to help alleviate potential controversy regarding what is included or not included in the contractor’s bid and baseline schedule. For example, the schedule basis may reflect a global approach for applying non-work days for anticipated lost weather days. The schedule basis for an EPC oil and gas project assumed several non-work days due to inclement weather for the winter seasons of a three year construction period. The contractor identified non‑work days for the construction period, starting in May 2014 and ending in May 2017. The 7‑day workweek calendar assumed the following non-work days due to inclement weather:
- Two non-work days in November
- Three non-work days in December
- Four non-work days in January
- Four non-work days in February
- Two non-work days in March
- One non-work day in April
The schedule basis document also stated that the non-work days above were based on a 5-year statistical average of inclement weather based on local meteorological data provided by a governmental agency. Based on the above, for any given year, the contractor included a total of 16 non-work days for inclement weather for those construction activities forecasted during the November through April time period. If a project is delayed beyond its planned duration, the schedule basis should be updated to reflect the non-work days that extend past the original planned construction period.
4.5 CAMP SIZE CONSIDERATIONS
When labor camps are required, they may become a significant factor in the success or failure of a project. If the camps are not sized correctly at the outset, the project completion date may slip due to camp accommodation limitations. Furthermore, any delays in constructing and achieving full occupancy of the camps may delay the effective start of construction work for permanent plant facilities because the camps are where the construction workers reside.
The contract documents should identify the party responsible for estimating the size of the labor camp. In making the decision regarding the camp size, the EPC contractor must identify its total direct and indirect labor, supervision, and management team to be housed in onsite camps. Within its baseline CPM schedule file, the resource loading of the EPC contractor’s labor resources should identify the planned labor hour requirements for its work force, assuming that the schedule file is properly resource loaded. In addition, the owner’s requirements for accommodation of its management and labor forces should also be identified, including an allowance for potential growth in the owner personnel requirements. When preparing a schedule basis for a large and complex EPC project that requires camps, the contractor and owner should pay close attention to camp sizing issues.
4.5.1 Camp Sizing Considerations
Several variables affect the required size of a labor camp, including factors such as: equipment and material quantities, direct and indirect labor ratios, workforce productivity, early dates versus late dates, third-party accommodations, and contingencies for potential workforce increases. These issues are further discussed below:
- Quantities of work to be installed – The starting point for camp sizing is an estimate of the quantities of equipment and materials to be installed, such as items of engineered equipment, meters of piping, cubic meters of concrete, number of instruments, tons of fabricated structural steel, etc. If estimated quantities are sufficiently accurate and fall within the contingencies used for the camp sizing calculations, then the camp sizing will not be in error due to underestimates or overestimates of quantities. However, if the quantities of equipment and materials used to define labor requirements are understated, the camp size will be similarly underestimated. The schedule basis must identify and document the estimated quantities along with any contingency factors used for the CPM schedule.
- Ratio of indirect labor to direct labor – The estimate of indirect labor to direct labor is a variable that is often inaccurate at the bidding stage. Definitions of indirect and direct labor vary between contractors. A portion of the labor hours that some contractors include in direct labor may be considered indirect labor hours by other contractors. The schedule basis should document the ratio of indirect labor to direct labor used for schedule development. To the extent that more indirect labor is required, the camp sizing may be accurate for the direct labor but significantly underestimated for the indirect labor. The schedule basis memorandum should document the assumptions regarding the ratio of indirect labor to direct labor.
- Productivity of the workforce used to install the estimated quantities – The estimate of productivity at site is a critical factor in estimating the required size of the construction camps. Even if estimates of quantities and the required ratio of direct and indirect labor are correct, errors in estimating on-site productivity will lead to errors in camp size calculations.
Contactor camp size estimates are more accurate when they are based on productivity estimates by craft rather than overall project average productivities. This is particularly important when considering that some crafts’ peak workloads occur later in the project than do other craft peaks. For example, instrumentation and electrical work is heavily back-end loaded, whereas civil work is heavily front-end loaded. To the extent that the EPC contractor has historical productivity data by craft in the jobsite location, the estimates of camp size requirements should be based on by-craft productivities rather than on overall site average productivity. A productivity analysis that discusses the above should be a major section within the schedule basis document.
- Early start vs. late start manpower loadings – The peak labor requirements are usually much higher when calculated on a late start basis from the CPM schedule than they would be if calculated on an early start basis. This could negatively alter the camp requirements if the EPC contractor decides to work toward the late dates in the CPM schedule. If an EPC contractor chooses to work toward late dates, it may become physically impossible to complete the work due to camp size limitations. It is recommended that a section in the schedule basis be devoted to analysis of potential camp size limitation problems due to early versus late dates.
- Numbers, timing, and durations of third parties requiring on-site accommodations – A difficult task in estimating the required camp size is forecasting the number, distribution over time, and durations of accommodations for third parties such as pre-commissioning, commissioning and start-up staff, and vendor service staff. These third parties are typically required toward the end of construction, and the accommodation plan for third party personnel may be planned on the basis that direct and indirect construction personnel will have de-staffed sufficiently by the time that the third parties are needed on site to avoid the need to add beds specifically for the third parties. To the extent that project delays may defer the actual de-staffing of construction direct and indirect labor forces, the camp may be undersized when it becomes necessary to house the third parties. A detailed study of third party personnel requirements is recommended for the Schedule Basis.
- Contingency for increases in base personnel requirements – A major unknown factor in camp sizing calculations is the allowance for camp size increases due to future changes that will add work scope to a project. Assuming that all of the contractor’s original camp sizing assumptions and calculations were accurate, the camp will be undersized if and when changes occur that must be accomplished when the construction staff is at or near peak loading. If change orders add ten percent to the original work scope man-hours during peak staffing periods, the ten percent more beds cannot be accommodated without delaying the project if the camp is undersized. The schedule basis memorandum should consider and provide a discussion of this potential issue.
Camp sizing calculations are complex for any construction project. However, accurately sizing the camp is one of the most important factors in achieving success on a project. Errors in estimating one or more factors may have compounding impacts, and camp sizing can become a limiting factor in achieving on-time construction performance. On some projects, these issues can be mitigated by use of houseboats, floatels, and the like as emergency housing measures during peak staffing periods if the site is near a body of water, but the unit cost of these accommodations is higher than land-based camps. It is recommended that the schedule basis address these issue and both the contractor and owner reach agreement on the basis for mitigating potential schedule delays and impacts.
4.6 CAMP CATERING AND OTHER SERVICE CONSIDERATIONS
Camp size increases after the initial design and construction of the camps involve more than just adding beds in housing units. The personnel occupying the beds require the same services as do the base loading personnel for which the camps were originally sized. Cooking, catering, laundry, potable water supply, sewage treatment, and recreational facilities are often bottlenecks when camp sizes need to be increased during a project. If the camps are undersized, the most likely outcome will be an overall project delay that keeps construction, pre-commissioning, commissioning, and start-up personnel on site for longer than originally planned. Delays in de-staffing the camps will likely lead directly to increases in catering and similar costs. Typically, the EPC contractor is responsible for following risks:
- Catering and other service risks for increases in quantities due to the contractor’s estimating errors prior to contract award.
- Increases in labor and supervision resulting from lower than planned productivity due to the contractor’s estimating errors and/or performance problems.
- Growth in catering and other service quantities attributable to the contractor’s delays.
In consideration of the above, the schedule basis memorandum should be utilized to document the initial rationale regarding assumptions, allowances, or exclusions included in the contractor’s baseline or updated schedule file. It is recommended that both the contractor and owner jointly review and adjust the schedule basis for camp catering and other service considerations.
5. CONCLUSIONS
The schedule basis memorandum is broadly defined as a written document that describes, explains, and details how the CPM schedule was developed at a specific point in time. The quality and reliability of the CPM schedule is directly tied to the thoroughness and completeness of the schedule basis memorandum which documents the planning rationales, assumptions, allowances, and exclusions. The schedule basis memorandum is a living document that may need updating from time-to-time during the course of a project’s lifecycle when conditions are warranted.
It is not unusual, however, for a contractor to prepare and submit an overly general or vague schedule basis memorandum that does not provide an adequate level of detail or supporting rationale necessary to fully understand how the CPM schedule was developed. In extreme cases, a contractor may not prepare any form of written schedule basis in support of its CPM schedule. If a CPM schedule analysis determines that it lacks a well-organized and documented schedule basis, then it is possible that legitimate changes to the initial schedule basis plan may be lost and construed as contractor scheduling deficiencies resulting in disputes that could have been avoided.
Large and complex EPC projects contain a number of inherent risks that can negatively affect the success of the project. Notable issues include overly optimistic labor productivity factors, competing projects, owner review and approval issues, inclement weather considerations, and camp size and camp catering issues. It is recommended that the EPC contractor and owner thoroughly analyze these issues and document the results in the schedule basis memorandum. The success or failure of the time management of large and complex EPC projects may depend on the quality and detail of the supporting documentation contained in the schedule basis memorandum.
About the Author
Ronald J. Rider, M.B.A., is a Senior Principal with Long International and has over 30 years of experience in construction project management and contract dispute resolution. Mr. Rider has performed CPM schedule development, project cost control, cost and labor hour variance modeling, impact identification and causation, change order pricing and resolution, retrospective schedule delay, time extension and acceleration analyses, concurrent delay assessments and damages quantification. Mr. Rider’s experience includes petrochemical, oil refinery, power, commercial, industrial, road/highway, transit, hospital/medical, airport and casino projects. He holds a B.S. degree in construction management from Colorado State University and an M.B.A. degree from the University of Colorado. Mr. Rider is based in the Denver, Colorado area and can be contacted at rrider@long-intl.com and (303) 346-5836.
1 Project Management Institute’s PMBOK® Guide, Fourth Edition, 2008, Chapter 6, page 129.
2 AACE International’s PS.18, Scheduling Management: Schedule Basis Memorandum, by H. Lance Stephenson, CCC, 2007 AACE International Transactions; and, AACE International’s Recommended Practice 38R-06, Documenting the Schedule Basis, June 18, 2009.
Copyright © Long International, Inc.
ADDITIONAL RESOURCES
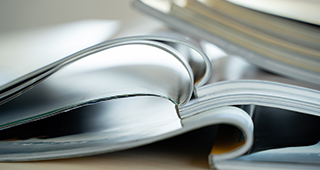
Articles
Articles by our engineering and construction claims experts cover topics ranging from acceleration to why claims occur.
MORE
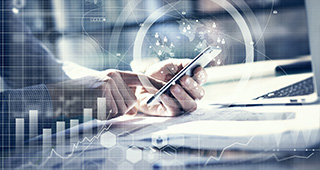
Blog
Discover industry insights on construction disputes and claims, project management, risk analysis, and more.
MORE
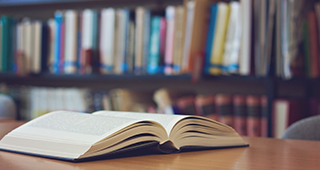
Publications
We are committed to sharing industry knowledge through publication of our books and presentations.
MORE